Lower capacity devices
- Dynamelt™ S Series
- Dynamelt™ D Series
- Simplicity™ Series
DYNAMELT™ SR
THE DYNAMELT™ SR ADHESIVE DISPENSING SYSTEM IS EASY TO INSTALL, OPERATE AND MAINTAIN THANKS TO ITS MODULAR DESIGN. ITS UNIQUE DESIGN AND PERFORMANCE FEATURES SET IT APART FROM THE COMPETITION AND TRANSLATE INTO MINIMISED DOWNTIME AND INCREASED APPLICATION FLEXIBILITY.

FLEXIBILITY
Its small footprint, ergonomic design and corner-mounted hose connections make it the most versatile and user-friendly melter on the market
RELIABILITY
Melt-On-Demand technology, a 15-fold increase in filter area and isolated electronics increase the reliability of this unit to a level that characterises the most robust melters on the market
SAFETY
A main power switch that ensures the power source is switched off and appropriately labelled, an insulated distributor cover and touch-protected electronics ensure safety during both production and maintenance
DYNAMELT™ SR-SERIES ADHESIVE DISPENSING SYSTEM
Dynamelt™ SR sets a new standard for innovation in the industry. Intuitive controls and a modular design simplify installation, operation and maintenance of the Dynamelt™ SR system, making it the first choice system for manufacturers worldwide. The system is designed to be used in conjunction with equipment from the Dynatec family to guarantee maximum efficiency and best performance, and is essentially ‘invisible’ – although it is visible to the eye, it is completely uncluttered. It uses 20% less energy and significantly less air than similar equipment. In addition, it is equipped with advanced diagnostics, allows for rapid component replacement and features a larger filtration surface area, significantly reducing maintenance cycles and labour required.
FEATURES
- Intuitive and easy to read display for quick checking of all system parameters can be set up on the front or side of the unit
- Uses 20% less energy and significantly less air than similar competing units, resulting in reduced operating costs
- New nanoceramic tank coating is five times more wear-resistant than competing PTFE coatings
- New simplified replacement procedures for modular electronics, filters and pumps
OPTIONS
- Analogue or digital pressure gauge
- Low glue level sensor
- In-line regulator with display
- Transformer 480 V AC
- Heating grille (S10 only)
TECHNICAL SPECIFICATIONS
System | S05 | S10 |
Tank capacity* | 5 kg | 10 kg |
Weight | 59 kg | 63 kg |
Operating temperature range | 10–218°C | |
Viscosity range | 500–50 000 mPas/cps | |
Melting capacity** | 10 kg/h. | 10 kg/h. |
Gear pump sizes | 1.5/3.2/4.5 cm3/rpm. | |
Piston pump performance | 0,91 kg/min |
MELT-ON-DEMAND TANK
Glue breakdown is considered to be the main cause of downtime for hotmelt adhesive equipment. To solve this problem, ITW Dynatec has patented the ‘Melt-On-Demand’ system. ITW Dynatec’s vertical, non-heated tanks only melt the amount of adhesive required for a specific application. The majority of hot-melt adhesive in the tank is still at a much lower temperature and may even be solid. Melting only the required amount of adhesive also offers additional benefits, i.e. faster start-up, reduced energy costs, improved viscosity control and reduced fumes.
Piston pump ratio | 12:1 | |
Hose/head outlet zones | 2, 4 or 6 | |
Max. hydraulic operating pressure | 68 bar (1 000 psi) | |
Supply voltage configuration 1 | 200–240 V AC, 1 phase, ∆, 50/60 Hz; 200–240 V AC, 3 phases, ∆, 50/60 Hz | |
Supply voltage configuration 2 | 240–400 V AC, 3 phases, Y, 50/60 Hz | |
Height | 533 mm (20,96″) | |
Deepth | 427 mm (16,8″) | |
Width | 655 mm (25,79″) | |
* Without the optional grating fitted ** Melting capacity depends on the type of adhesive |
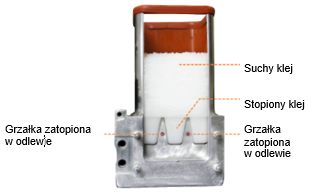
DYNAMELT™ D
THE MELT-ON-DEMAND TANK USED ON THE DYNAMELT™ D SAFELY AND EFFECTIVELY REDUCES DOWNTIME AND ALSO SPEEDS UP COMMISSIONING, REDUCES ENERGY COSTS, IMPROVES VISCOSITY CONTROL, REDUCES FUMES AND MINIMISES MAINTENANCE WORK.
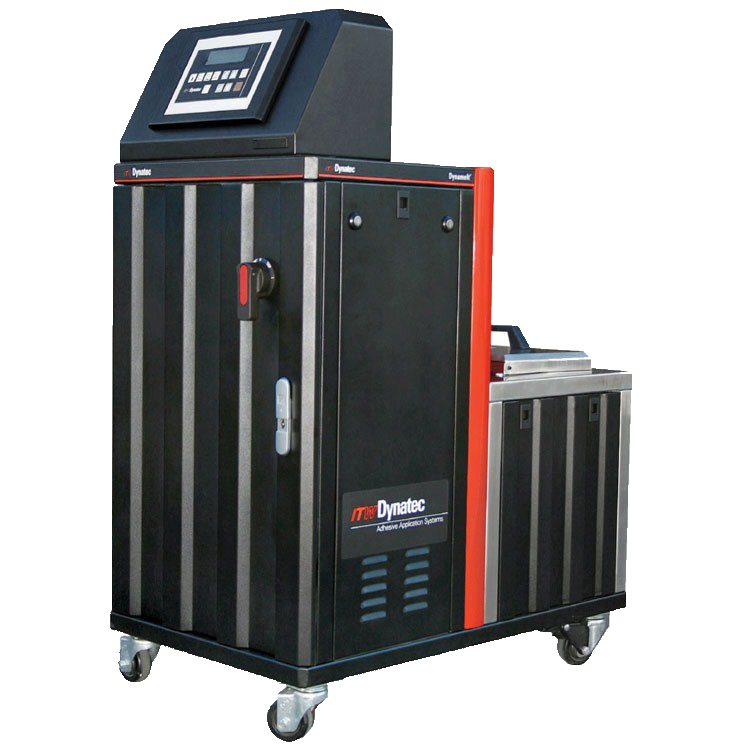
SIMPLICITY
Touchscreen/LCD control panel simplifies operation
FLEXIBILITY
Up to 8 standard hoses/heads can be connected
RELIABILITY
Melt-On-Demand tank extends adhesive life and increases efficiency
DYNAMELT™ D-SERIES ADHESIVE DISPENSING SYSTEM
For the Dynamelt S-series system, a choice of four different tank sizes and a double or single gear pump is available. The unit uses a microprocessor-based temperature controller to tightly control the temperature of the hotmelt glue fed to up to eight hose outputs: standard and precision metered.
FEATURES
- Up to four drives / four gear pumps provide up to eight metered outputs
- Standard and precision metered outputs available
- User-friendly control via touchscreen or LCD display in multiple languages, including Chinese
- DynaControl™ P.I. digital temperature controller with accuracy typical of platinum sensors
- 10 combinations of tank size and melting capacity
OPTIONS
- High-precision gear pumps
- Low adhesive level indicator
- Digital speed readout (RPM)
- KBSI signal isolator
- Communication via Ethernet protocol
- Analogue or digital glue pressure indicator
- In-line regulator
- AUX/temperature zones
TECHNICAL SPECIFICATIONS
System | D25 | D45 | D50 | D90 |
Tank capacity* | 25 kg | 45 kg | 50 kg | 90 kg |
Operating temperature range | 38–218°C | |||
Viscosity range (reduced melting capacity) | 1000–50 000 cps (50 000–100 000 cps) | |||
Melting capacity** | 23 kg/h. | 46 kg/h. | ||
Melting capacity with optional grating** | 41 kg/h. | 82 kg/h. | ||
Melting capacity with 2 optional gratings** | – | 59 kg/h. | – | 118 kg/h. |
Gear pump sizes | 1,5/3,2/4,5 cm3/rpm. | |||
Number of gear pumps per machine | 1–2 | 1–4 | ||
Hose/head outlet zones | 2–6 | 2–8 | ||
Max. hydraulic operating pressure | 68 bar (1000 psi) | |||
Supply voltage configuration 1 | 200–240 V AC, 3 phases, 50/60 Hz | |||
Supply voltage configuration 2 | 380–400 V AC, 3 phases, Y, 50/60 Hz | |||
Operator interface | Keyboard with icons | Keypad with LCD | ||
Maximum power | 24 200 W | 26 700 W | 48 400 W | 53 400 W |
Height | 1330 mm (52,4″) | 1330 mm (52,4″) | ||
Deepth | 975 mm (38″) | 975 mm (38″) | ||
Width | 520 mm (20,5″) | 1040 mm (41″) | ||
* Without the optional grating fitted ** Melting capacity depends on the type of adhesive |
SIMPLYCITYT™
THE SIMPLICITY™ ADHESIVE DISPENSING SYSTEM IS EASY TO INSTALL, OPERATE AND MAINTAIN THANKS TO ITS MODULAR DESIGN. ITS UNIQUE DESIGN AND PERFORMANCE FEATURES SET IT APART FROM THE COMPETITION AND TRANSLATE INTO MINIMISED DOWNTIME AND MAXIMISED APPLICATION FLEXIBILITY AND RELIABILITY.
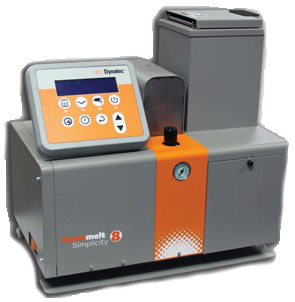
SIMPLICITY
Intuitive V6 controls and clear, easy-to-read display
EFFICIENCY
Patented Melt-On-Demand™ technology melts only the necessary adhesive
RELIABILITY
Fewer nozzle clogs reduce maintenance work and downtime
SIMPLICITY™ ADHESIVE DISPENSING SYSTEM
The Simplicity™ adhesive dispensing system takes innovation, technology and performance to a whole new level. Clear, intuitive V6 controls and a modular design make the system easy to install, operate and maintain. In this compact unit distinguished by its new ceramic orange coating, the HMI and tank lid are rotatable to provide configuration flexibility. In turn, with its small internal tank and automatic feeding system, the unit effectively competes with ‘tankless’ systems. To optimally meet production needs, a pre-melt grid can be fitted (16 kg tank only) to increase glue melting capacity and two piston pumps can be fitted to double the feeding rate – making Simplicity™ a unique machine in its class.
FEATURES
- The ability to leave the unit on unattended provides invaluable benefits
- Vertically positioned pump equipped with Easy-Spin pump filter
- Thanks to easy operation via a single control board, no lengthy training is required
- Melt-On-Demand technology eliminates charring and reduces maintenance work
- Dual piston pump performance (only on 16 kg units)
- Complex filter/regulator with integrated pre-filter and coalescing filter
OPTIONS
- Various tank sizes: 4, 8 and 16 kg
- 400 V AC or 480 V AC without earth transformers
- Low level sensor
- Pressure gauges in front of the filter indicate when the filter needs to be changed or when the nozzle is clogged
- Operation of the Dynafill automatic feed system
- Supports up to 6 hoses
- Pre-melting grid available to increase melting capacity
TECHNICAL SPECIFICATIONS
System | 4KG | 8KG | 16KG / 16KG Dual Piston Pump |
Tank capacity | 4 kg | 8 kg | 16 kg |
Operating temperature | 10–232°C | ||
Melting capacity* | 11,3 kg/h. | 11,3 kg/h. | 22,7 kg/h. |
with optional grille | N/A | N/A | 4,8 kg/h. |
Piston pump performance | 4/8/16KG = 0,91 kg/min | ||
Piston pump ratio | 12:1 | ||
Hose/head outlet zones | 2, 4, 6 | ||
Max. hydraulic operating pressure | 68 bar (1000 psi) | ||
Stability of temp. control | ±1°C | ||
Supply voltage configuration | 230 V AC, 1 phase; 240 V AC, 3 phases, Δ; 230/400 V AC, 3 phases + N + PE; 400/480 V AC, 3 phases, Δ | ||
Working viscosity | 500–50 000 cps | ||
Height | 454,5 mm (17,89″) | 541,5 mm (21,32″) | 510,6 mm (20,10″) |
Deepth | 339 mm (13,34″) | 339 mm (13,34″) | 431,2 mm (16,97″) |
Width | 619,5 mm (24,39″) | 619,5 mm (24,39″) | 712,9 mm (28,07″) |
* Depending on adhesive type |
MELT-ON-DEMAND TANK
Glue breakdown is considered to be the main cause of downtime for hotmelt adhesive equipment. To solve this problem, ITW Dynatec has patented the ‘Melt-On-Demand’ system. ITW Dynatec’s vertical, non-heated tanks only melt the amount of adhesive required for a specific application. The majority of hot-melt adhesive in the tank is still at a much lower temperature and may even be solid. Melting only the required amount of adhesive also offers additional benefits, i.e. faster start-up, reduced energy costs, improved viscosity control and reduced fumes.
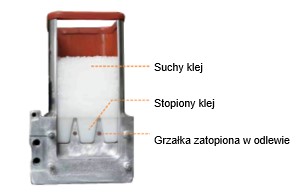